Rapid Axis for Tooling and Molding
With experience in Injection Molding, Die Casting and Urethane Casting, Rapid Axis is the subject matter expert on a vast array of tooling and molding requirements spanning various industries, processes and materials.
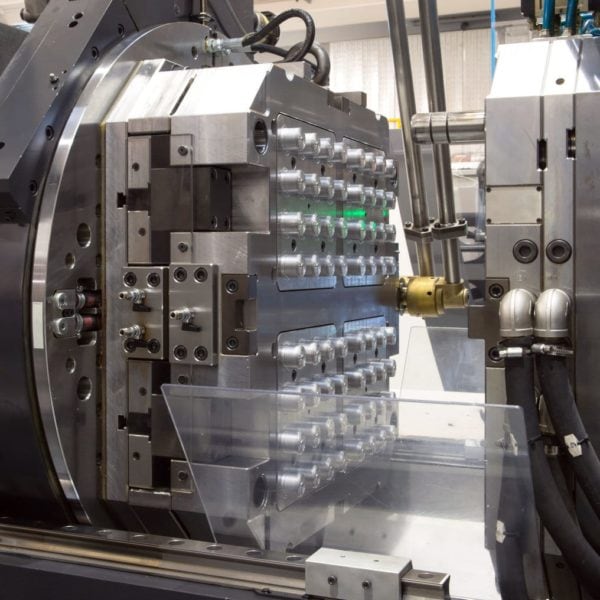
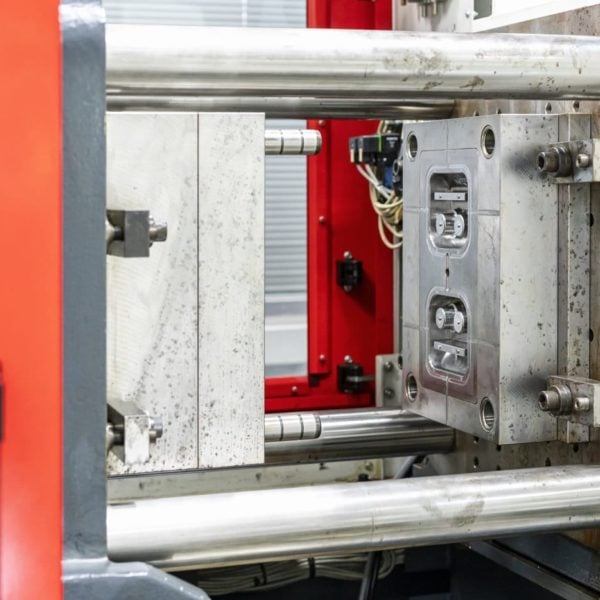
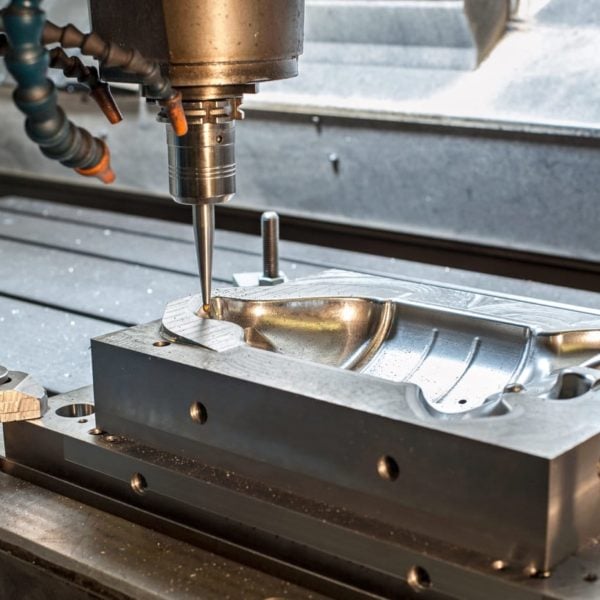
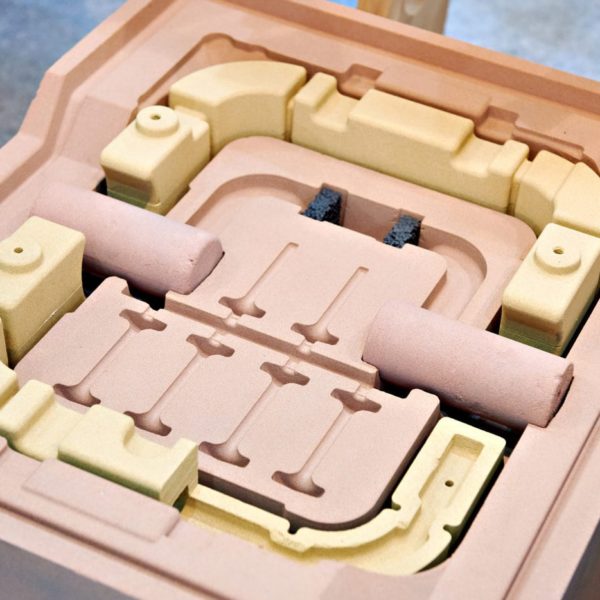
Why Rapid Axis is the best choice for Tooling and Molding
Experience in rapid deployment of tooling for a variety of applications including prototyping, short run production and mass production make Rapid Axis the easy choice for any of your tooling and molding needs. We can deploy injection molds in a matter of business days, die cast tooling in a matter of weeks and urethane casting tooling in as quickly as a few days. See why companies like Rivian, Thermo Fisher and Cue Health keep coming back for molding projects and reach out to a member of our staff today.
High repeatability
Low part cost after initial investment
Excellent quality parts
What are Tooling and Molding?
The terms tooling and molding are pretty general within the world of manufacturing. As you’ll see in subsequent sections, this can refer to anything from making cut-outs in a web of material to creating millions of consumer goods.
From a manufacturer’s perspective, tooling and molding give customers the opportunity to repeatedly make identical units. These units could be sold to the public, used during your in-house operation, or sold to other companies.
The overarching theme is that we fabricate something that allows you to quickly and cost-effectively make repeated parts.
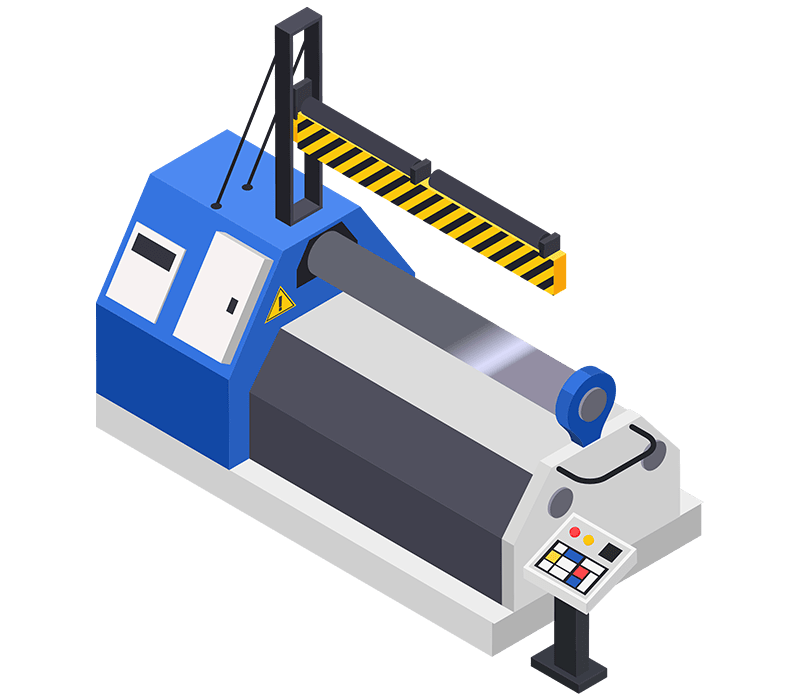
Different Types of Tooling and Molding
There are a few different styles of tooling and molding options offered at Rapid Axis. Here are some quick definitions to get you started — but feel free to navigate to their individual pages to learn more.
Urethane Casting
Urethane casting is the low-volume equivalent to injection molding. In this option, a soft mold is filled with a liquid version of a flexible or rigid plastic. This can include urethane, elastomers or silicone.
The mold is formed around a 3D Printed master pattern to create a negative of the object you’re making. The liquid fills up this negative and is then cured. From there, the mold gets opened and the part is removed, leaving you with a solid product made out of urethane.
Die Casting
Another option is called die casting. This entails pushing molten metal into cavities built in a metal die. One half of the die is typically fixed on the machine, and the other half is removable. With the molten metal inside, the two halves are clamped together and wait for the metal to cool and harden.
The halves are removed, and pins help push the cast part out of the mold.
Injection Molding
Injection molding is the industry standard when it comes to mass-producing consumer parts. A metal mold is filled with molten product. The product can be either metal, plastic, rubber, elastomers, and most polymers.
Once in the mold, the part will fill the cavities and create a product. It sits for a little bit and cools before an ejector mechanism takes the cooled part out of the mold and allows the chamber to accept more molten product to create another unit.
Stamping and Die Cutting
The simplest way to describe stamping and die cutting is to compare them to cookie cutters. It uses the outline of the desired shape with sharp edges. A person will push the cutter into the cookie, and the result is a heart-shaped cookie, for example.
This same theory extends to any form of low-strength webs of material, like rubber or cloth. You can use a stamp or die cutter to cut out identical units from a large web.
We fabricate the “cookie cutter” in this example, per the specs in your application.
Tooling and Molding Applications
These different terms and styles of tooling and molding might seem confusing. The good news is that these concepts are pretty universal, so they’re easy to conceptualize once we explain them further. To help out, let’s review some of the common applications and benefits of this form of fabrication.
Mass-Produce a Product
Tooling and molding gives you the best opportunity to mass-produce a product, hands-down. There are no other options on the market that can compare to the speed, efficiency, and cost of injection molding, for example.
Compared to 3D printing and CNC machining, this technology is orders of magnitude faster and less expensive.
If you run a business that needs to make a million units per year, injection molding will make it easy.
Expedite the Fabrication Process
One way that mass-production is easy with tooling and molding is because it expedites the process. Depending on your part and application, you can make a part in an injection molder within seconds.
If you look around your room at the different consumer products you have lying around, there’s a good chance that most of them are injection molded or die-cast. It’s the only option that allows companies to flood the market with their product.
Dedicated injection molding machines run around the clock, 24/7/365. The only way this is possible is with high-quality molds and inserts from experts like our team at Rapid Axis. Going with a low-quality machine shop to make the molds will mean wasted time, money, and effort on your part.
Keep Your Costs Low
Once a tooling and molding operation is set up, the per-unit cost is minuscule. The biggest cost is the upfront money required for the tooling and machine itself. Over time, these costs dilute as more units are produced.
For instance, we had a project that made units for pennies each once the machine was running. These same parts were sold for more than $10 on the open market once our customer received the order.
Stress-Free Way to Get Parts
At Rapid Axis, we have in-house injection molding machines. We can take you from an initial 3D-printed prototype all the way to mass-produced parts without the need to shop outside.
If you were to purchase your own injection molding machine and tool, you could be looking at half a million dollars at the end of the day. With dedicated tooling shops, you can save a fortune and focus on getting high-quality parts delivered to your loading dock.
We’ll keep your tooling and molding safe here, and you’ll just let us know when you need another production run and how many units you need. We’ll handle the rest.